What does Lean Management mean?
Lean Management is a global method of continuous improvement that aims to maximize value while minimizing waste and optimizing operational efficiency.
The basic concept of Lean Management is to create value by eliminating all activities that do not add value to the product or service. To achieve this, the Lean Management method relies on a number of principles, such as rational inventory management, just-in-time production, continuous improvement, process standardization, employee involvement and the use of analytical tools and methods to identify potential sources of improvement.
Lean Management is often associated with the manufacturing industry, where it was first developed, but it can also be applied in other sectors, such as services, healthcare, finance, etc.
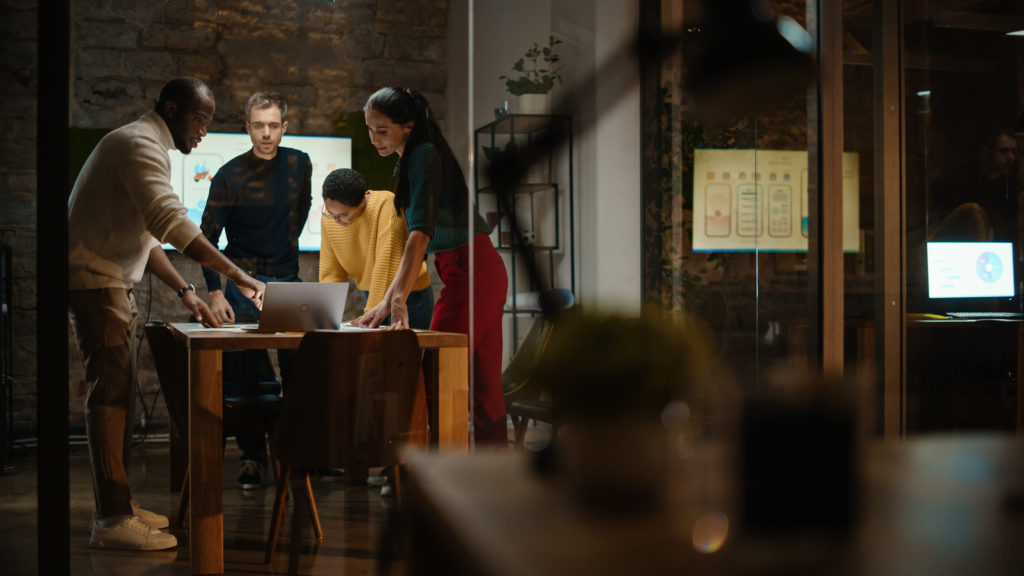
The principles of Lean Management
There are many Lean Management principles. Here are a few of the most important:
- Value creation (for the customer): Lean Management aims to deliver the best possible value to the customer by eliminating all activities that do not add value to the product or service.
- Elimination of waste: Lean Management identifies sources of waste in production or service processes, then eliminates or reduces them wherever possible.
- Continuous improvement: Lean Management encourages the constant improvement of production or service processes through reflection, experimentation and innovation.
- Process standardization: Lean Management seeks to standardize production or service processes to minimize variations and errors.
- Just-in-time: Lean Management organizes production or service processes into continuous, demand-driven flows.
The tools of Lean Management
- Kaizen: A continuous improvement method that encourages employees to identify and solve everyday problems.
- Just in time: A system that aims to produce or supply exactly what the customer needs, when the customer needs it.
- 5S: A method of organization and cleaning designed to improve efficiency and safety in the workplace.
- Value chain mapping: A tool for visualizing production or service stages and identifying sources of waste.
- Poka-Yoke: An error prevention system designed to eliminate human error and production defects.
- SMED (Single Minute Exchange of Die): A method aimed at reducing the time between different production stages.
Why use Lean Management?
In general, Lean Management, if correctly applied, is beneficial and virtuous for the company. It helps to improve productivity, quality and performance by acting on various factors.
Quality improvement: By identifying sources of waste and implementing more efficient processes, Lean Management can reduce errors and production defects, and improve the overall quality of products and services.
Reduce costs: By eliminating non-value-adding activities and optimizing processes, Lean Management reduces production costs and improves profitability.
Increase customer satisfaction: By creating greater added value for customers, and meeting their expectations more quickly, Lean Management improves customer satisfaction and loyalty.
Improved productivity: By optimizing processes, Lean Management increases overall productivity, which can lead to improved company results.
Improved corporate culture: Lean Management encourages employee participation in process improvement, which strengthens team commitment and motivation, and fosters a corporate culture based on innovation, continuous improvement and collaboration.
In short, Lean Management helps to optimize production processes, increase quality, reduce costs and increase customer satisfaction, while fostering an improved corporate culture and enhanced employee productivity.
How to implement Lean Management ?
Implementing Lean Management requires a methodical, step-by-step approach.
It involves identifying the objectives and key processes that need to be optimized. This often involves mapping the value chain to identify sources of waste and opportunities for improvement.
The next step is to ensure that all employees are aware of the issues and are trained to take an active part. An awareness-raising program must be organized to explain Lean Management concepts and provide employees with the skills needed to identify sources of waste and improve processes.
Implementing Lean Management implies a culture of continuous improvement, in which employees are encouraged to identify problems and propose solutions for improvement. It is important to create a working environment where employees feel comfortable sharing their ideas and suggestions.
Lean Management requires the use of specific tools and techniques such as Kanban, 5S, Kaizen and Poka-Yoke. It is important to select the tools best suited to the company’s processes and practices, and to adapt them to specific needs.
It is essential to monitor the results of implementing Lean Management, so as to measure improvements in real time and adjust the methods and tools used.
The implementation of Lean Management must be sustainable and part of a long-term approach. This often means implementing visual management practices, ongoing training and regular communication to ensure that processes continue to evolve and improve.
Implementing Lean Management requires a methodical approach, based on the identification of key objectives, employee training, the establishment of a continuous improvement culture, the use of specific lean tools, the monitoring of results and the sustainability of Lean Management practices.
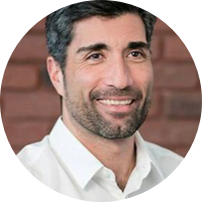
CTO de Yumana